BI_51
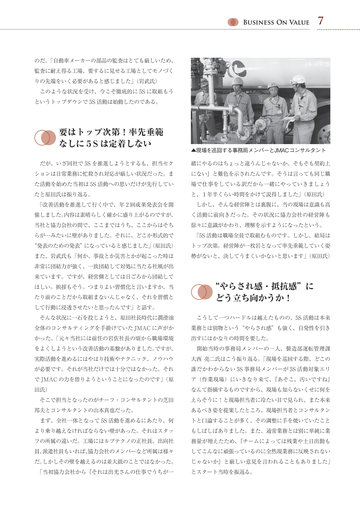
- ページ: 7
- 7
のだ。 「自動車メーカーの部品の監査はとても厳しいため、 監査に耐え得る工場、要するに見せる工場としてモノづく りの先端をいく必要があると感じました」 (岩武氏) このような状況を受け、今こそ徹底的に 5S に取組もう というトップダウンで 5S 活動は始動したのである。
要はトップ次第!率先垂範 なしに5S は定着しない
だが、いざ同社で 5S を推進しようとするも、担当セク ションは日常業務に忙殺され対応が厳しい状況だった。ま た活動を始めた当初は 5S 活動への思いだけが先行してい たと原田氏は振り返る。 「改善活動を推進して行く中で、年 2 回成果発表会を開 催しました。 内容は素晴らしく確かに盛り上がるのですが、 当社と協力会社の間で、ここまではうち、ここからはそち らが…みたいに壁がありました。それに、どこか形式的で “発表のための発表” になっていると感じました」 (原田氏) また、岩武氏も「何か、事故とか災害とかが起こった時は 非常に団結力が強く、一致団結して対処に当たる社風が出 来ています。ですが、経営側としては日ごろから団結して ほしい。挨拶もそう。つまりよい習慣化と言いますか、当 たり前のことだから取組まないんじゃなく、それを習慣と して行動に浸透させたいと思ったんです」と話す。 そんな状況に一石を投じようと、原田社長時代に潤滑油 全体のコンサルティングを手掛けていた JMAC に声がか かった。 「元々当社には前任の岩佐社長の頃から職場環境 をよくしようという改善活動の基盤がありました。 ですが、 実際活動を進めるにはやはり技術やテクニック、ノウハウ が必要です。それが当社だけでは十分ではなかった。それ で JMAC の力を借りようということになったのです」 (原 田氏) そこで担当となったのがチーフ・コンサルタントの芝田 邦夫とコンサルタントの山本真也だった。 まず、全社一体となって 5S 活動を進めるにあたり、何 より乗り越えなければならない壁があった。それはスタッ フの所属の違いだ。工場にはルブテクノの正社員、出向社 員、 派遣社員もいれば、 協力会社のメンバーなど所属は様々 だ。 しかしその壁を越えるのは並大抵のことではなかった。 「当初協力会社から『それは出光さんの仕事でうちが一
▲現場を巡回する事務局メンバーとJMACコンサルタント 緒にやるのはちょっと違うんじゃないか。そもそも契約上 にない』と難色を示されたんです。そうは言っても同じ職 場で仕事をしている訳だから一緒にやっていきましょう と、1年半くらい時間をかけて説得しました」 (原田氏) しかし、そんな経営陣とは裏腹に、当の現場は意識も高 く活動に前向きだった。その状況に協力会社の経営陣も 徐々に意識がかわり、理解を示すようになったという。 「5S 活動は職場全員で取組むものです。しかし、結局は トップ次第。経営陣が一枚岩となって率先垂範していく姿 勢がないと、決してうまくいかないと思います」 (原田氏)
“やらされ感・抵抗感”に どう立ち向かうか!
こうして一つハードルは越えたものの、5S 活動は本来 業務とは別物という“やらされ感”も強く、自発性を引き 出すにはかなりの時間を要した。 開始当時の事務局メンバーの一人、製造部運転管理課 大西 亮二氏はこう振り返る。 「現場を巡回する際、どこの 誰だかわからない 5S 事務局メンバーが 5S 活動対象エリ ア(作業現場)にいきなり来て、 『あそこ、汚いですね』 なんて指摘するものですから、現場も知らないくせに何を えらそうに!と現場担当者に冷たい目で見られ、また本来 あるべき姿を提案したところ、現場担当者とコンサルタン トと口論することが多く、その調整に手を焼いていたこと もしばしばありました。また、通常業務とは別に単純に業 務量が増えたため、 『チームによっては残業や土日出勤も してこんなに頑張っているのに全然現業務に反映されない じゃないか』と厳しい意見を言われることもありました」 とスタート当時を振返る。
- ▲TOP