ビジネスインサイツ64
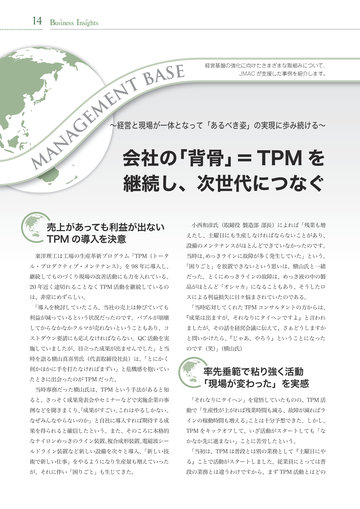
- ページ: 14
- 14
経営基盤の強化に向けたさまざまな取組みについて、 JMAC が支援した事例を紹介します。
〜経営と現場が一体となって「あるべき姿」の実現に歩み続ける〜
会社の 「背骨」 = TPM を 継続し、次世代につなぐ
売上があっても利益が出ない TPM の導入を決意
東洋理工は工場の生産革新プログラム「TPM(トータ ル・プロダクティブ・メンテナンス) 」を 98 年に導入し、 継続してものづくり現場の改善活動にも力を入れている。 20 年近く途切れることなく TPM 活動を継続しているの は、非常にめずらしい。 「導入を検討していたころ、当社の売上は伸びていても 利益が減っているという状況だったのです。バブルが崩壊 してからなかなかクルマが売れないということもあり、コ ストダウン要請にも応えなければならない。QC 活動を実 施していましたが、目立った成果が出ませんでした」と当 時を語る横山真喜男氏(代表取締役社長)は、 「とにかく 何かほかに手を打たなければまずい」と危機感を抱いてい たときに出会ったのが TPM だった。 当時専務だった横山氏は、TPM という手法があると知 ると、さっそく成果発表会やセミナーなどで実施企業の事 例などを聞きまくり、 「成果がすごい。 これはやるしかない。 なぜみんなやらないのか」と自社に導入すれば期待する成 果を得られると確信したという。また、そのころに本格的 なナイロンめっきのライン装置、 複合成形装置、 電磁波シー ルドライン装置など新しい設備を次々と導入、 「新しい技 術で新しい仕事」をやるようになり生産量も増えていった が、それに伴い「困りごと」も生じてきた。 小西和彦氏(取締役 製造部 部長)によれば「残業も増 えたし、土曜日にも生産しなければならないことがあり、 設備のメンテナンスがほとんどできていなかったのです。 当時は、 めっきラインに故障が多く発生していた」という。 「困りごと」を放置できないという思いは、横山氏と一緒 だった。とくにめっきラインの故障は、めっき液の中の製 品がほとんど「オシャカ」になることもあり、そうしたロ スによる利益損失に日々悩まされていたのである。 「当時応対してくれた TPM コンサルタントの方からは、 『成果は出ますが、それなりにタイヘンですよ』と言われ ましたが、その話を経営会議に伝えて、さぁどうしますか と問いかけたら、 『じゃあ、やろう』ということになった のです(笑) 」 (横山氏)
率先垂範で粘り強く活動 「現場が変わった」を実感
「それなりにタイヘン」を覚悟していたものの、TPM 活 動で「生産性が上がれば残業時間も減る、故障が減ればラ インの稼動時間も増える」 ことは十分予想できた。しかし、 TPM をキックオフして、いざ活動がスタートしても「な かなか先に進まない」ことに苦労したという。 「当初は、TPM は普段とは別の業務として『土曜日にや る』ことで活動がスタートしました。従業員にとっては普 段の業務とは違うわけですから、まず TPM 活動とはどの
- ▲TOP