ビジネスインサイツ66
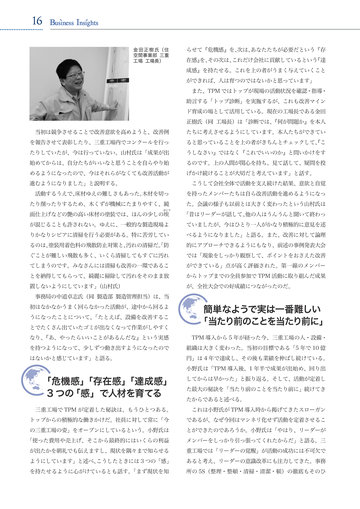
- ページ: 16
- 16
金 田 正 樹 氏( 住 空間事業部 三重 工場 工場長)
らせて『危機感』を、 次は、 あなたたちが必要だという『存 在感』 を、 その次は、 これだけ会社に貢献しているという 『達 成感』を持たせる。これを上の者がうまく与えていくこと ができれば、人は育つのではないかと思っています」 また、TPM ではトップが現場の活動状況を確認・指導・ 助言する「トップ診断」を実施するが、これも改善マイン ド育成の場として活用している。現在の工場長である金田 正樹氏(同 工場長)は「診断では、 『何が問題か』を本人
当初は競争させることで改善意欲を高めようと、改善例 を報告させて表彰したり、三重工場内でコンクールを行っ たりしていたが、今は行っていない。山村氏は「成果が出 始めてからは、自分たちがいいなと思うことを自らやり始 めるようになったので、今はそれらがなくても改善活動が 進むようになりました」と説明する。 活動するうえで、 床材ゆえの難しさもあった。 木材を切っ たり削ったりするため、木くずが機械にたまりやすく、鏡 面仕上げなどの艶の高い床材の塗装では、ほんの少しの埃
ほこり
たちに考えさせるようにしています。本人たちができてい ると思っていることを上の者がきちんとチェックして、 『こ うしなさい』ではなく『これでいいのか』と問いかけをす るのです。上の人間が関心を持ち、見て話して、疑問を投 げかけ続けることが大切だと考えています」と話す。 こうして会社全体で活動を支え続けた結果、意欲と自覚 を持ったメンバーたちは自ら改善活動を進めるようになっ た。会議の様子も以前とは大きく変わったという山村氏は 「昔はリーダーが話して、 他の人はうんうんと聞いて終わっ ていましたが、今はひとり一人がかなり積極的に意見を述 べるようになりました」と語る。また、改善に対して論理 的にアプローチできるようにもなり、前述の事例発表大会 では「現象をしっかり観察して、ポイントをおさえた改善 ができている」点が高く評価された。第一線のメンバー からトップまでの全員参加で TPM 活動に取り組んだ成果 が、全社大会での好成績につながったのだ。
が混じることも許されない。ゆえに、一般的な製造現場よ りかなりシビアに清掃を行う必要がある。特に苦労してい るのは、 塗装用着色料の飛散防止対策と、 汚れの清掃だ。 「防 ぐことが難しい飛散も多く、いくら清掃してもすぐに汚れ てしまうのです。みなさんには清掃も改善の一環であるこ とを納得してもらって、綺麗に掃除して汚れをそのまま放 置しないようにしています」 (山村氏) 事務局の中道卓志氏(同 製造部 製造管理担当)は、当 初はなかなかうまく回らなかった活動が、途中から回るよ うになったことについて、 「たとえば、設備を改善するこ とでたくさん出ていたゴミが出なくなって作業がしやすく なり、 『あ、やったらいいことがあるんだな』という実感 を持つようになって、少しずつ動き出すようになったので はないかと感じています」と語る。
簡単なようで実は一番難しい 「当たり前のことを当たり前に」
TPM 導入から 5 年が経った今、三重工場の人・設備・ 組織は大きく変わった。当初の目標である「5 年で 10 億 円」は 4 年で達成し、その後も業績を伸ばし続けている。 小野氏は「TPM 導入後、1 年半で成果が出始め、回り出 してからは早かった」と振り返る。そして、活動が定着し た最大の秘訣を「当たり前のことを当たり前に」続けてき たからであると述べる。 これは小野氏が TPM 導入時から掲げてきたスローガン であるが、なぜ今回はマンネリ化せず活動を定着させるこ とができたのであろうか。小野氏は「やはり、リーダーが メンバーをしっかり引っ張ってくれたからだ」と語る。三 重工場では「リーダーの覚醒」が活動の成功には不可欠で あると考え、リーダーの意識改革にも注力してきた。事務 所の 5S(整理・整頓・清掃・清潔・躾)の徹底もそのひ
「危機感」 「存在感」 「達成感」 3 つの 「感」で人材を育てる
三重工場で TPM が定着した秘訣は、もうひとつある。 トップからの積極的な働きかけだ。社員に対して常に「今 の三重工場の姿」をオープンにしているという。小野氏は 「使った費用や売上げ、そこから最終的にはいくらの利益 が出たかを朝礼でも伝えますし、現状を隅々まで知らせる ようにしています」と述べ、 こうしたときには 3 つの「感」 を持たせるように心がけているとも話す。 「まず現状を知
- ▲TOP