佐賀エレクトロニックス株式会社
- 生産・ものづくり・品質
ダントツ工場に挑戦する全員参加のものづくり活動
売り上げダウンにリストラ......。再起不能かと思われた佐賀製作所は、今や業界関係者の工場見学が後を絶たない「ダントツ工場」になりつつある。3年で生まれ変わったものづくりの現場で、何が行われていたのか。
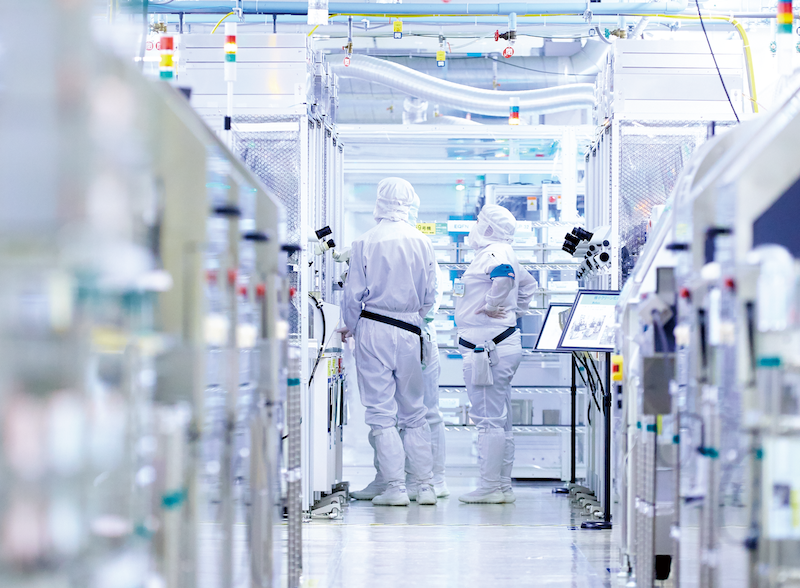
課題・ミッション
- 5Sが仕組みになり、文化になる
- 一人前の工場からダントツ工場へ
- 市場の変化に対応できるものづくり
- 全員参加による改善活動
「現場をきれいにすることがゴールではない」と掲げ、将来を見据えた5S活動に着手。また、半導体製造現場の根幹である設備管理への意識を高め、全設備のOEE※80%達成へ。従業員のモチベーションを高め、継続していく仕組みづくりとは。
※OEE(Overall Equipment Effectiveness:設備総合効率)
「目的に合った5S」こそ本当に取り組むべきこと
1980年代中頃の半導体といえば日本が世界のトップを走り、技術力、製造能力、シェアなど半導体業界にとっては興隆を極めた時代だった。佐賀エレクトロニックスも同様。製作所では主に半導体の「後工程」を専門に行い、工場の増設を重ねるなど、業績は右肩上がり。ところがリーマンショック後、業績は悪化。2012年には約600人いた従業員を200人近くまで縮小し、売り上げも年間億単位のペースで落ちていった。
現在の林社長が現職に就任したのは、そんな状況が続く2015年。工場内は人がおらず、設備もまともに動かない。誰もが疲弊し、先が見えないような状況だったという。今は見違えるような現場に生まれ変わったが、当時はお客さまからもポジティブな言葉はいただけなかったそうだ。
「もう一度5S(整理・整頓・清掃・清潔・躾)から、と考えましたが、5Sといっても響かない。ものづくりの現場では当たり前の基礎ですが、それすらできていませんでした。それは、従業員のモチベーションが上がらないからでもありました。実は、2015年にわずかですが黒字化しました。親会社の業務だけでなく、他社の受託生産も始めることになり、『改善活動をするなら今しかない!』と、2016年から第一製造部が中心となり、改善活動をスタートさせました」(林さん)
実は、林社長はすでに頭の中にダントツ工場に向けたステップの構想があった。ゴールは「従業員の幸せ」や「お客さまの満足」「取引先や地域との共生」、そして「社会貢献」。それを実現するために「土台(=前提条件)」「1階(=一人前の工場)」「2階(=ダントツ工場)」と分け、それを下からしっかりと積み上げていくイメージだった。
「土台は5Sが当たり前に浸透している状態。そして整った人事制度と従業員の意識の向上。これができなければ、1階も2階もつくれません。実現するために、ものづくりの将来を見据えた5S活動を行うために、JMACにコンサルティングをお願いしました」(同)
代表取締役社長 林 力 さん
林社長に響いたのは、JMACの藤井が提唱する「考える5S」という手法。つまり「目的に合致した5S」のことである。単に「整理整頓をしましょう、ものを減らしましょう」という5Sとは別ものだ。
「私たちの工場で問題になるのは『異物』です。それも10マイクロメートルの塵。なぜ5Sを行うのか。それは塵を排除するためです。これが目的に合致した5Sです。なぜ発塵するか、なぜ持ち込まれてしまうのか。これを徹底的に究明し、改善しました。何のために整理整頓するのか、なぜ清掃が必要なのか、目的が明確だと行動も明確になります。これが"継続していく仕掛け"なんですね」(同)
しかし、目的が明確でも「全員参加」で推進していくのはやはり難しい。そこで、第一製造部 製造技術課の深町さんをリーダーに、事務局を設置。ここでも、「考える5S」推進の策が練られた。
全員がリーダーになり自分の言葉で語る
「全員参加型の意識改革というプロジェクトは、なかなか難しいとは思ったのですが、社長に『好きなようにやっていい』と言われ、信頼をしていただいたのはうれしかったです。好きにしていいという押し付けではないやり方に、みんなもついてきてくれたという面もあります。
もともと『当事者意識が足りない』というのが課題でした。リーダーが替わったら改善したものが元に戻ってしまうのでは意味がありません。ルールが根づかないのは、仕組みになっていないからです。そこで、シーズンごとにリーダーを替える方法をとりました。成功する人も失敗する人もいますが、苦労をした人は、次のリーダーを必ず助けます。その人材を、1人ずつ増やしていきました。リーダーは自分で咀嚼し、自分の言葉で伝えなければなりません。これを繰り返すことで、仕組みになっていきました」(深町さん)
第一製造部 製造技術課 課長 深町 憲宏 さん
工場の廊下は見事というしかない。改善の取り組みはすべて見える化され、リーダーはわかりやすい資料を作成。それを全員でシェアする。工場見学に来るお客さまにもそれは開示され、改善プロジェクトの進捗状況もわかるようになっている。
「廊下にはゴミまで展示しています。対策を練っても、微細な塵は出現する。とことん追求していることを、ぜひ見ていただきたい」(同)
実はこの「考える5S」は、技術と照らし合わせて行わないと成功しない。残すもの、処分するものを判断するのも技術への深い理解がなければできない。指定席管理にも技術のノウハウがあってこそ。この5S活動を繰り返すことで、全員の技術への理解が深まったことが、企業価値向上へとつながっている。
「この活動で、埋もれていた人材や意外な才能があらわになることがあります。社員の実力を垣間見る機会にもなり、たいへん価値ある取り組みになりました」(同)
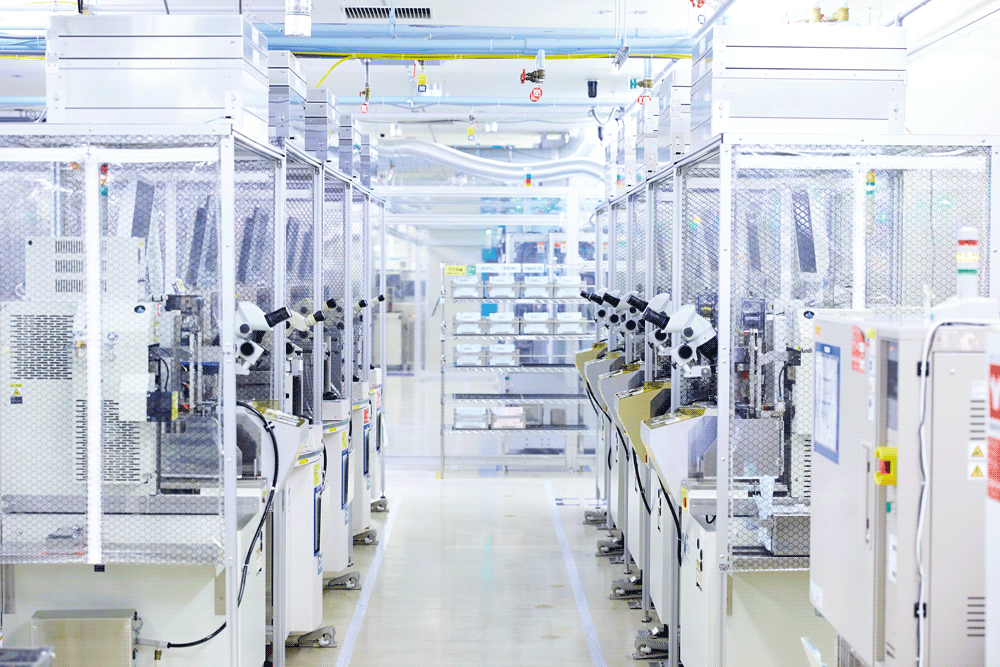
いよいよダントツ工場へ 2年目の設備管理
考える5S活動は、1年で定着した。次の年からは社長の構想にあった次のステップ、つまりダントツ工場に向けた取り組みが始まった。
「半導体は、ほぼ機械がつくります。設備こそが品質向上の鍵。ですから私は、設備管理に関わるチームには、彼らの存在の重要性を説き、プライドをもってほしいと伝えてきました。設備管理こそ、私たちの企業価値を上げる根幹です。そこには、設備管理者やオペレーターの『感度』があります。色や匂い、手の感覚の違和感を感じられるのは人ですから、誇りをもって自分の仕事に邁進してほしいと伝えました」(林さん)
このステップで採用されたのが藤井の「既知・曖昧・未知」というメカニズム分析。
「既知というのは、原因がわかっているけど着手できていないエラー。曖昧とは、なんとなく原因がわかっているけど検証ができていないもの。この2つは点検の強化で改善できます。未知は何が原因かさっぱりわからないものです。これは個別改善が必要になります。設備トラブルを減らすために、この3層に分けて考えるという手法を導入しました。これは私たちには今までにない発想で、大学の研究室で行うアプローチだそうです。仮説を立てて調査・検証し、仮設のための分析をして、技術的に一つひとつつぶしていきます。これは"ノウハウの手の内化"になり、技術的探究のやりがいにもつながっています。将来的には、既知の領域を70%まで押し上げることを目標にしています」(田中さん)
第一製造部 IC設備課 課長 田中 稔彦 さん
愚直な活動で現場が成長 工場そのものが商品に
たった3年で劇的な変化を遂げた要因として、全員参加としたことと、達成感を感じる仕掛けが大きかった。
「仕掛けといっても特別なことではなく、ほめたりほめられたりという場があれば、誰でもうれしくなりま
すよね。目標さえわかっていれば、あとはそこに向かう方法を否定せずに愚直にやってみる。これが私たちの行った活動です」(深町さん)
現在の工場には、自動車、関連部品の担当者が毎週のように訪れる。かつてはほめられることが少なかったというが、今は工場を見て、受注が決まるほど。営業担当も、積極的にお客さまを工場案内するという。
「お客さまから工場をほめられるのは、うれしいですね。現在、生産の主力はタイですが、マザー工場として、われわれにしかつくれない部品が受注できています」(林さん)
劇的な変化の裏舞台は、「愚直に、地道に、徹底的にやる」という熱意に支えられている。
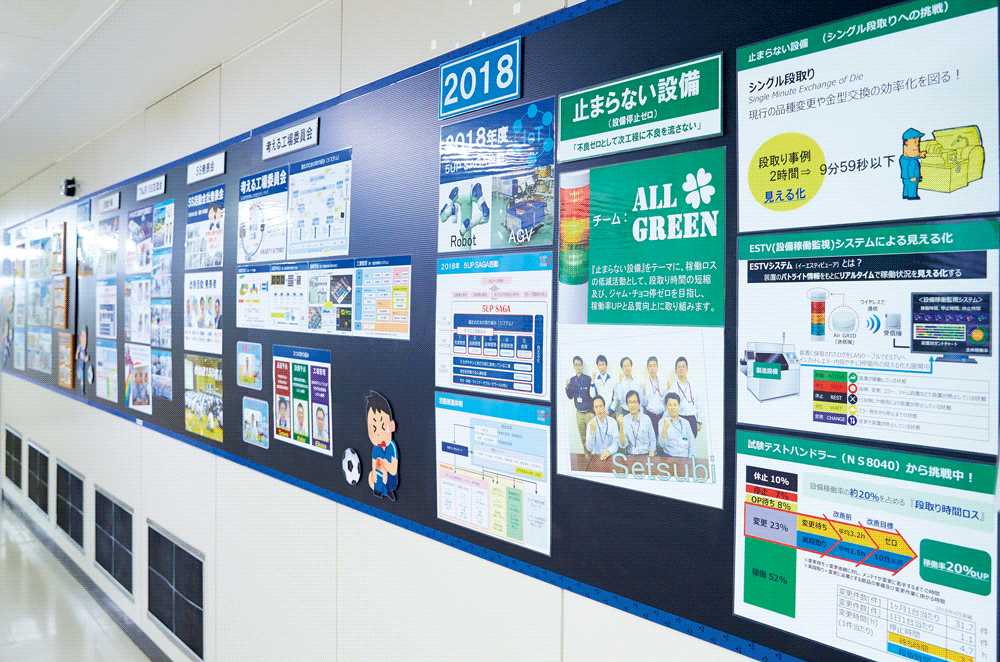
JMACコンサルタントEYE(担当コンサルタントからの一言)
愚直な取り組みでダントツ工場へ
現場の改善活動には、合理的アプローチが必要です。たとえば、5Sでも後戻りしないようにステップを分けたり、「なぜそれをやるのか」を全員で考えて共有する仕組みです。今回の「考える5S」は、小さな成功体験を積み重ねつつ、社長方針の実現に向けた活動となりました。「愚直に取り組む」文化がダントツ工場の礎となっています。
藤井 広行(シニア・コンサルタント)
本稿はBusiness Insights Vol.72からの転載です。
社名・役職名などは取材当時のものです。
関連コンサルティング・サービス
生産・ものづくり・品質
生産現場の人、設備、材料、製造方法とマネジメントシステムを改善して生産性向上をはかります。生産現場は製品特性や製法により多種多様の特性を持つ複雑系です。そのため私たちは、現場でじっくり見て聞いて、フィットする特別な改善プログラムを作ることから仕事を始めます。少しだけ時間はかかりますが、そのことは現場力を高め、現場の一人ひとりが成長を感じられる魅力的な職場になることを知っているからです。