大建工業株式会社
- 生産・ものづくり・品質
- その他
「改善マインド」の育成で 工場の持続的成長を目指す 〜「成果の見える化」でモチベーションを高め、活動を定着〜
熱心な改善活動で一度は成果が出るものの、モチベーションが維持できず、定着には至らない----改善活動に取り組む企業が一度はぶつかるであろう"マンネリ化"の壁は、思いのほか高い。大建工業・三重工場は、その壁を打開すべく2012年にTPMを再導入し、活動を刷新した。5年が経った今、三重工場の人・設備・組織は大きく変わり、業績も順調に伸長している。悩みの種だった"マンネリ化"を解消して活動を定着させ、さらにスパイラルアップし続けている秘訣はどこにあるのか。生産現場における改善マインドの育成方法を中心に、活動への想いと今後の展望を伺った。
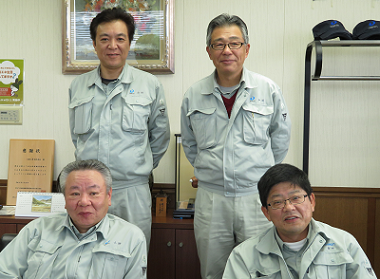
"マンネリ化"を解消し、 改善活動の壁を突破する
大建工業は住宅用建材メーカーとして1945年(昭和20年)に創業し、70余年もの間、新素材・新技術の開発に挑戦し続けてきた。今回取材で伺った三重県津市の三重工場は、木材を使った床材の製造に特化している。一口に床材と言っても実に多種多様で、大理石のような質感と美しさを追求した鏡面仕上げの床材や、木材組織にプラスチック樹脂を注入した高強度の床材など、住環境のあらゆるシーンに対応している。
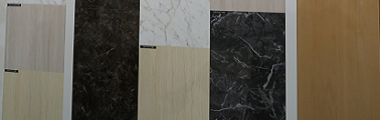
三重工場では、50年ほど前から生産性向上に向けた改善活動を続けてきた。そのときどきで最適だと考える活動をいくつか実施してきたが、いずれも一時的に成果が出るものの、なかなか成果を持続できないことが悩みでもあった。1990年代には独自にTPM活動をしていたが、2000年代に入ってからはそれもまた徐々に停滞していった。前工場長の小野世生氏(住空間事業部 三重工場 工場長付)は「当時、会社の利益目標自体はクリアできていましたが、活動がマンネリ化し、目に見える改善がされていないところに問題を感じていました」と振り返る。小野氏とともに改善活動を主導してきた山村文明氏(同 製造部長)は「かつてわれわれが第一線で現場にいた時代には、自主保全のための技能を一生懸命習得して、それを現場で伝承していました。しかし年を重ねるにつれ伝承も滞りがちになって、現場の人たちがだんだん設備に弱くなってきたという悩みがありました。『やっているけど、なかなかうまくいかないね』という感じでした」と当時の状況を説明する。
この状況を打開するため、小野氏は三重工場独自の目標を掲げることにした。「三重工場を預かっている以上、何らかの形で『ナンバーワンの工場』を目指そうではないかと。そこで、月生産量を増やして床材シェアNo.1になろう、その効果は5年で10億円のプラスだということで『5年で10億円を達成し、業界No.1工場となる』という目標をつくりました」(小野氏)。そのためには何をすべきかの項目をつくっていく中で、「これをやるにはやはり TPMがいいだろう」と考えた小野氏は、JMAC支援のもと活動を進めることに決めた。TPM(Total Productive Maintenance/全員参加の生産保全)は、製造企業が持続的に利益を確保できる体質づくりをねらいとしており、最適なツールだった。
こうして、三重工場はJMACをパートナーとしてTPMの導入・推進に向けて動き出した。
「目からウロコのTPM」 幹部を鍛え直して再発進!
TPM導入を決めたのち、まず行ったのは「幹部の鍛え直し」だ。小野氏は「今までの改善活動では、『さあ今日からやりましょう』と言っても、メンバーもリーダーもその上司も、みんな同じようなレベルでした。それがすぐにマンネリ化する原因だと考え、導入にあたっては活動を引っ張る立場の人間に『TPMとはどういうものか』を徹底的に学ばせました」と説明する。
実際にJMACのTPMカレッジコースに通った山村氏は「最初は『知っていることなのに、なぜ講習を受けなくてはいけないのかな』と思っていました。それまで独自にやっていたTPMのイメージでいたので、『自主保全だけ』という考えで行ったのですが、ロスは生産現場だけではなく管理・間接部門なども含めた工場全体で考えるべきであると改めて認識しました」と語る。こうして導入準備に1年をかけたのちの2013年6月、三重工場は本格的にTPMをスタートした。
活動のスタートにあたり、まず行ったのは推進体制の整備だ。「自主保全」「品質保全」などの活動ごとに6つの部会をつくり、リーダーが現場から選んだメンバーに教育していく。これとは別にリーダー全体の推進部会も設けた。
そしていよいよ迎えたキックオフの日----入念な準備をしてきた上層部の思いとは裏腹に、メンバーたちの反応は「これまでも改善活動をしてきたのに、またやるの?」というものだった。しかし彼らは、その3年後に始まった事例発表大会(大建工業グループ小集団活動事例発表大会)で改善事例が評価され、全社で第1位を受賞するまでになった。いったい、この日から今日までの間に、三重工場ではどのような活動をし、その中でメンバーたちはどう変わっていったのであろうか。
「一緒にやる」「時間をとる」がメンバーの心と体を動かす
当初、モチベーションを持てずにいたメンバーの動きは停滞しがちで、活動は思うように進まなかった。そこで山村氏は、自分たちが率先して動くことで彼らの動きを促していったという。「たとえば自主保全部会では、最初に我々が設備を点検・清掃して見せて、『初期清掃はこうするんですよ』と教えるのです。メンバーのモチベーションを上げるために、とにかく『一緒にやる』『繰り返し言う』ことを徹底しました」
また、生産現場の活動時間を確保するため、月に1回、機械を止める時間を設けるようにした。「改善活動では『やりなさいと言われても時間がない』というのが現場の意見ですから、工場長に『1ヵ月に1度だけ機械を止めさせてください』と交渉し、時間内に少しでも活動できるような体制をつくりました」(山村氏)
当初は競争させることで改善意欲を高めようと、改善例を報告させて表彰したり、三重工場内でコンクールを行ったりしていたが、今は行っていない。山村氏は「成果が出始めてからは、自分たちがいいなと思うことを自らやり始めるようになったので、今はそれらがなくても改善活動が進むようになりました」と説明する。
活動するうえで、床材ゆえの難しさもあった。木材を切ったり削ったりするため、木くずが機械にたまりやすく、鏡面仕上げなどの艶の高い床材の塗装では、ほんの少しの埃が混じることも許されない。ゆえに、一般的な製造現場よりかなりシビアに清掃を行う必要がある。特に苦労しているのは、塗装用着色料の飛散防止対策と、汚れの清掃だ。「防ぐことが難しい飛散も多く、いくら清掃してもすぐに汚れてしまうのです。みなさんには清掃も改善の一環であることを納得してもらって、綺麗に掃除して汚れをそのまま放置しないようにしています」(山村氏)
事務局の中道卓志氏(同 製造部 製造管理担当)は、当初はなかなかうまく回らなかった活動が、途中から回るようになったことについて、「たとえば、設備を改善することでたくさん出ていたゴミが出なくなって作業がしやすくなり、『あ、やったらいいことがあるんだな』という実感を持つようになって、少しずつ動き出すようになったのではないかと感じています」と語る。
「危機感」「存在感」「達成感」3つの「感」で人材を育てる
三重工場でTPMが定着した秘訣は、もうひとつある。トップからの積極的な働きかけだ。社員に対して常に「今の三重工場の姿」をオープンにしているという。小野氏は「使った費用や売上げ、そこから最終的にはいくらの利益が出たかを朝礼でも伝えますし、現状を隅々まで知らせるようにしています」と述べ、こうしたときには3つの「感」を持たせるように心がけているとも話す。「まず現状を知らせて『危機感』を、次は、あなたたちが必要だという『存在感』を、その次は、これだけ会社に貢献しているという『達成感』を持たせる。これを上の者がうまく与えていくことができれば、人は育つのではないかと思っています」
また、TPMではトップが現場の活動状況を確認・指導・助言する「トップ診断」を実施するが、これも改善マインド育成の場として活用している。現在の工場長である金田正樹氏(同 工場長)は「診断では、『何が問題か』を本人たちに考えさせるようにしています。本人たちができていると思っていることを上の者がきちんとチェックして、『こうしなさい』ではなく『これでいいのか』と問いかけをするのです。上の人間が関心を持ち、見て話して、疑問を投げかけ続けることが大切だと考えています」と話す。
こうして会社全体で活動を支え続けた結果、意欲と自覚を持ったメンバーたちは自ら改善活動を進めるようになった。会議の様子も以前とは大きく変わったという山村氏は「昔はリーダーが話して、他の人はうんうんと聞いて終わっていましたが、今はひとり一人がかなり積極的に意見を述べるようになりました」と語る。また、改善に対して論理的にアプローチできるようにもなり、前述の事例発表大会では「現象をしっかり観察して、ポイントをおさえた改善ができている」点が高く評価された。第一線のメンバーからトップまでの全員参加でTPM活動に取り組んだ成果が、全社大会での好成績につながったのだ。
住空間事業部 三重工場 工場長
金田 正樹氏
簡単なようで実は一番難しい 「当たり前のことを当たり前に」
TPM導入から5年が経った今、三重工場の人・設備・組織は大きく変わった。当初の目標である「5年で10億円」は4年で達成し、その後も業績を伸ばし続けている。小野氏は「TPM導入後、1年半で成果が出始め、回り出してからは早かった」と振り返る。そして、活動が定着した最大の秘訣を「当たり前のことを当たり前に」続けてきたからであると述べる。
これは小野氏がTPM導入時から掲げてきたスローガンであるが、なぜ今回はマンネリ化せず活動を定着させることができたのであろうか。小野氏は「やはり、リーダーがメンバーをしっかり引っ張ってくれたからだ」と語る。三重工場では「リーダーの覚醒」が活動の成功には不可欠であると考え、リーダーの意識改革にも注力してきた。事務所の5S(整理・整頓・清掃・清潔・躾)の徹底もそのひとつだ。山村氏は「毎日の定点撮影を通じて、『この状態でいいと思いますか』と問いかけをしながら、毎日忘れずに少しずつ動くことの大切さを伝えてきました」と振り返る。
金田氏は、三重工場にとってTPMは「やるべきことを系統だってやるための手段であり、成果をしっかりと見せるための道具である」と説明する。「前回のTPMでは、初期清掃などの作業にこだわるあまり、自分たちの姿が見えていませんでした。しかし今回は、闇雲にやって自分たちが今どこにいるのかわからないということがない。最後の目標がしっかりあって、途中の工程の成果もはっきり見えるので、それが本人たちのモチベーションにつながったのだと思います。この成果を測る手段を明示してくれたのが、今回のTPMの一番いいところだと思っています」
JMACのTPMコンサルタント・西原政美は「当たり前のことを当たり前にという大建工業さんのスタンスは、TPMの自主保全にマッチしています。当たり前をコツコツ進めていきながら、現場での改善意欲、改善のアイデアや発想が生まれる土壌もあるのが特徴」と見ている。
住空間事業部 三重工場 前工場長、現工場長付
小野 世生氏
目指すは"ダントツ"No.1! 新時代の床材開発に挑戦
「5年で10億円」を4年で達成し、床材シェアNo.1となった今、三重工場の新たな目標は単なるNo.1ではない、さらに差をつけた「業界ダントツNo.1」の工場になることだ。そのため、現在はTPM活動と並行して設備の強化も進めている。設備を入れ替えながら、一部設備については増設も視野に入れ、さらなる生産性向上をねらう。
今後の経営課題について金田氏は「このTPM活動をいかに伝承・定着して続けていくかが課題です。前回のようにマンネリ化して続かなくなるということがないように、まさに最初のスローガンである『当たり前のことを当たり前に』を10年後もやり続けることが大切だと思っています」と述べる。また、「マンネリ化したときに何を変えていくかが重要である」ともいい、「ポイントは、会社の利益目標などの方針とTPMをうまくブレンドして、『自分たちのありたい姿』をはっきり明示するところにあると考えています。全グループの生産目標に照らし合わせると、三重工場はこれから2割以上生産量を上げていかなければなりません。それが何年でできるかを見えるようにすると、10年後の姿も見えてきます。最終的に日本でダントツNo.1の工場になるという想いがありますので、それに向かって改善し続けるのみです」
小野氏は「ダントツNo.1になるためには、シェアだけではなく、商品においても他社より抜きんでたものがないといけない。今後は新しい床材開発にも挑戦し、目標達成に向けて全社一丸となって取り組んでいきたいと考えています」
「当たり前のことを当たり前に」----TPM活動で培った改善マインドと全社一丸のパワーは、近い将来、三重工場をダントツNo.1へと導くに違いない。
担当コンサルタントからの一言
あるべき姿の工場のイメージを全員で共有する
TPMの自主保全は「何事も徹底する」という姿勢がないと定着しません。たとえば、定置化、見える化など、やれることをとことん徹底するということです。そのためにはトップダウンとボトムアップをうまく回す必要がありますが、大建工業・三重工場のトップの方々は、そのやり方が非常にうまいですね。現場をひっぱりながら、現場の主体性を生かしています。あるべき工場の姿をトップから現場の従業員まで共有している点も評価できます。そのせいか、現場の改善意欲が高く、改善のアイデアや発想に、いつも驚かされます。さらに要因を突き止める力(解析力)を向上させれば、もっと大きな成果が出るはずです。
西原 政美(TPMコンサルタント)
※本稿はBusiness Insights Vol.66からの転載です。
社名・役職名などは取材当時のものです。
関連コンサルティング・サービス
生産・ものづくり・品質
生産現場の人、設備、材料、製造方法とマネジメントシステムを改善して生産性向上をはかります。生産現場は製品特性や製法により多種多様の特性を持つ複雑系です。そのため私たちは、現場でじっくり見て聞いて、フィットする特別な改善プログラムを作ることから仕事を始めます。少しだけ時間はかかりますが、そのことは現場力を高め、現場の一人ひとりが成長を感じられる魅力的な職場になることを知っているからです。