三菱ケミカル株式会社
- 生産・ものづくり・品質
- 化学
三菱ケミカル・豊橋事業所は2009年、TPM活動を本格スタートした。その後、地道な活動を続け、この10年で設備の故障件数は14分の1に激減した。その背景には、「オペレーターと専門保全員の二人三脚」「製造部長と課長の活動をクロスさせる」といった独自の取組みがあった。それらはどのように行われ、そのとき人はどう変わっていったのか。息の長い活動を続ける秘訣とは。そして昨年、次世代の担い手を育成する「保全道場」がスタート、新たな挑戦が始まった。今回、10年にわたる活動の軌跡と今後の展望を伺った。
「故障を減らす」 工場の命題をTPMで解決
三菱ケミカルは2017年4月、三菱化学・三菱樹脂・三菱レイヨンの3社の統合により発足し、素材から機能商品まで幅広いフィールドで事業を展開している。
今回取材で訪れた豊橋事業所には、旧三菱レイヨンの工場がある。その広大な敷地面積は東京ドーム10個分にも及び、今から57年前の1962年(昭和37年)に創業した。ポリプロピレン繊維の製造からスタートした工場は、その後、炭素繊維(写真)、中空糸膜、アクリル樹脂フィルムと事業を順次拡大し、今では4つの事業を展開する工場となった。
製造現場の生産性を上げるためには、「いかに設備の故障を減らし、ラインの停止を防ぐか」が重要となる。そのため、豊橋事業所では昔から、さまざまな故障削減の改善活動に取り組んできた。しかし、その成果も次第に下げ止まってきたことから、2009年、JMAC支援のもとTPM(Total Productive Maintenance)を本格スタートした。TPMは、製造企業の持続的な利益確保のために、継続的に人材育成や現場改善を実施する仕組みをつくる。
本活動を主導してきた宮森隆雄氏(執行役員 豊橋事業所長)は、1999年から豊橋事業所の製造部で故障削減活動に取り組んでいたが、途中2007年から2011年まで他の事業所にいたため、TPMが始まった当初は参画していない。だからこそ「2012年にここに戻ってきたとき、TPMがかなり軌道に乗っていたので驚いた」と振り返る。
活動開始から10年が経った今、故障件数は当初の14分の1にまで激減した。いったい、この10年間でどのような取組みをしてきたのであろうか。
執行役員 豊橋事業所長 宮森 隆雄氏
「私つくる人、あなた直す人」から「自分の設備は自分で守る」へ
活動当初の様子について、TPMの立ち上げを工場で経験し、現在は事務局を務める品田勝彦氏(企画管理部 ものづくり力強化G グループマネージャー)はこう語る。「最初の頃は、オペレーターは『設備のトラブルがあったら保全を呼べ』という感じで、『私は動かす人で、壊れたら直すのが保全だ』という意識が強く、トラブルもロスも多かった」
この場合、「壊れたら直す」ではなく「故障を未然に防止」できれば、故障を減らすことができる。そのために行うのが、オペレーター自身が設備の清掃・点検を行う「初期清掃」だ。TPMではこうした活動を「自主保全」と呼ぶ。
実際の活動では、品田氏を含む管理職がまず「初期清掃とはどのようなものか」を体験し、それをオペレーターに教えていった。当初、メンバーの反応は「また新しい活動をやるの?」というものだったが、徐々にその意識は変わっていったという。品田氏は、「みんなで初期清掃をやって、汚れていた設備をキレイにして、不具合を発見できるようになったことで、大きなトラブルになる前に気づけるようになったのは非常に大きな成果でした」と語る。
宮森氏は、一歩踏み込んだ初期清掃から入って、徐々に装置に詳しくなり、意識が変わっていったところが非常によかったと述べる。「もともと『製造の人はつくるだけ』『故障は保全の人が対応する』ということが長年の文化になっていたので、最初にそこの意識の切り替えと覚醒ができたのは非常に大きかったと思います」
製造と保全の二人三脚で 「故障ゼロ」に挑む
その後は、さらなる故障削減のため、次のステップへと進んだ。専門保全員は日ごろ現場にいないため、オペレーターの報告を受けてから故障を直すことが多い。そのため、毎日設備に接しているオペレーターがいかに早く設備の異常に気づき、報告できるかが重要となる。
そこで、豊橋事業所で注力したのが「設備に強いオペレーター」の育成だ。オペレーターの設備への知識と点検技能の向上を図るため、専門保全員がそれぞれの装置に関しての知識をレクチャーしていった。宮森氏は、「製造課のメンバーは、図面を描いたりしながら、非常によく勉強していました。製造側の知識も上がりますし、設備技術側も『オペレーターはこういうところがわかっていなかったんだな』と知ることができ、お互いにしっかりがっちりとスクラムを組んで進めることができたと思います」と話す。また、「オペレーターの知識が上がるにつれ、現場の要求がより厳しくなってきたことで、設備技術側も『もっと高度なことをやっていかなければいけない』と感じているようです」と語る。
そして現在は、事前の「チャンス保全」に力を入れている。これは同事業所独自の呼び方であるが、品種切替えのタイミングなど、"運転を止めているチャンス"に保全するという取組みだ。オペレーターが事前に「異音が発生している」と設備の異常に気がついた時点で専門保全員に見てもらい、運転中の故障を減らす。宮森氏は、「われわれは運転中のブレイクダウンを減らすことを重視しています。現場の感度が上がり、ひどい破壊に至る前に保全できるようになったことで、故障が大幅に減少しました」と語る。
企画管理部 ものづくり力強化G グループマネージャー 品田 勝彦氏
リーダーの「信念」と「情熱」が活動を牽引し、成功に導く
活動が成功している背景は、この保全体制の強化のほかにもう1つある。全員参加の意識を醸成する体制づくりだ。豊橋事業所では独自に、2つの方法を取り入れている。
まず1つ目は、製造現場の活動をAタイプ・Bタイプに分けている。装置を使うオペレーターの活動をAタイプ、装置を使わない検査員の活動をBタイプとした。TPMでは製造部門が「なぜ自分たちだけ」という思いになることが少なくないが、検査部門も同じ熱量で作業改善に取り組むことで、全員参加のスタートが切れた。
2つ目は、4製造部長が専門分科会の会長を務めている。事業所全体の活動は、部長率いる4分科会「自主保全・品質保全・個別改善・革新分科会」を中心に行う。これにより、部長がトップ診断などで隣の工場を見る機会も増え、活動への参画意識が非常に強くなったという。
この分科会の中で特徴的なのが、製造課長および生産技術課長をメンバーとする「革新分科会」だ。現場の活動と事業部のテーマをタイムリーにリンクすることを目的として、2015年に立ち上げた。課長同士の横のつながりをつくり、レベルアップを図ることで、課長が転勤で入れ替わってもレベルをキープできる仕組みづくりでもある。
宮森氏は、「こうした活動は、リーダーが活動を信じ、情熱を持ってやらなければうまく進みません。TPMは"仕事とは別の余分なことをやっている"と思われがちなため、彼らにはいつも『TPMはあくまでも現場を良くするための"ツール"だから、うまく利用してほしい』と話しています。また、課長以下だけで活動すると、部長はどうしても傍観者になりがちです。その点、本活動では製造部長がリーダーシップを持って分科会を率い、課長もそこに入っていくという形でクロスさせているので、それがうまく運営できているポイントなのかなと思います」と語る。
「保全道場」で新人教育 次世代の担い手を育てる
TPM開始から10年が経った今、活動は定着し、故障件数は14分の1にまで激減した。豊橋事業所では、この体制を維持するために、毎年入ってくる新入社員の教育に注力している。その背景について宮森氏は、「昔の人はトラブルの多いときも知っているので、『今はかなり故障が減った』という実感があります。しかし、新入社員は故障が少ない状態で入って来るため、TPM のありがたみがよくわかっていない。ですから、まずは『TPM はこういう活動をやっている』ということを事務局がかなりしっかりと、数年間、定期的に研修しています」と説明する。
さらに、そのための実習設備である「保全道場」(写真)もつくった。モデル設備では、設備技術者からボルトの締め方、工具の使い方などを習いながら、実際に配管をばらす体験をする。また、危険予知能力を高めるために、「ローラーに巻き込まれたらどうなるか」を体験するコーナーもある。
これをつくるために、宮森氏はさまざまな実習設備を見学し、豊橋事業所に一番適した設備を模索したという。豊橋では繊維を巻くローラーを多用するため、そのモデルもセットした。宮森氏は、足掛け数年かけて完成させた保全道場への想いをこう語る。「昔は、トラブルを通して腕も知識も上げて、熟達していきました。しかし今は、トラブル自体が少ないため、それを体験できないと自信が持てず、怖さも知らないままになってしまいます。ですから、こういった実習設備は絶対に必要だと思ったのです」
保全道場で講師を務める品田氏は、こうした教育はとても重要であるとし、「今までの活動を後戻りさせず、さらに良くしていくために、この保全道場を活用して事業所の基盤をつくっていきたい」と熱く語った。
保全道場による教育について、JMACのTPMコンサルタント木村吉文・中西浩明は「自主保全と専門保全がうまく連携しながら、現場に必要なスキルをしっかり理解したうえで保全道場を整えていったので、教育効果も高いと思います。寿命を延ばす、修理間隔を延ばすために必要なスキル・知識の習得など、さらに道場の活用範囲が広がることを期待しています」と語る。
TPMは「人づくりの柱」 10年後を見据え、着実に歩む
宮森氏は、豊橋事業所が息の長いTPM活動を続けることができたのは、即効性よりも基礎体力を上げていくことに力点を置いてきたからだと語る。「『スピードアップして、ある期限までにこれを達成する』ということよりも、『持続的に定着させよう、焦らず確実にやっていこう』というスタンスでスタートしたことが大きいと思います。教育などへの取組みも、5年10年経ったときに必ず差が出てくるはずです。実際、10年前に比べるとわれわれの現場はずいぶん変わったようで、たまによその事業所の人が来たときに、『だいぶ変わりましたね』という言葉を聞くと嬉しいですね」
また、将来的には事務局主導ではなく、現場が自主的に活動できるような文化にしていきたいとも話す。「そういうことが各現場で代々受け継がれ、それが当たり前になるのが理想です。ただ、外部の刺激を入れて変化していくことも大事ですから、JMACさんにはこれからも、われわれの考えつかないような新鮮な視点を提供していただきたいですね」
そして豊橋事業所にとって、TPM は「人づくりの柱」であるとする。「私は、TPM自体は基本的には"人づくり"だと思っています。技術的なことだけではなく、ものづくりの文化をつくるうえで、TPM 活動を柱にしてやっていきたい。それに耐えうる活動であると私自身が信じていますし、TPMを通じて、現場改善などいろいろなことを楽しめるような形の人づくりになっていったらいいなと思いますね。モチベーションを持って活動に取り組めて、しかも仕事が楽になって、トラブルが減って残業も減る。これらはすべて働き方改革にもつながっていきますので、この活動をずっと続けていくことが大切だと思っています」
三菱ケミカルがTPMで得たのは、故障減の成果だけではない。そこには人と組織の大きな成長があった。そしてこれからも、次の10年を目指して一歩一歩、歩み続ける。
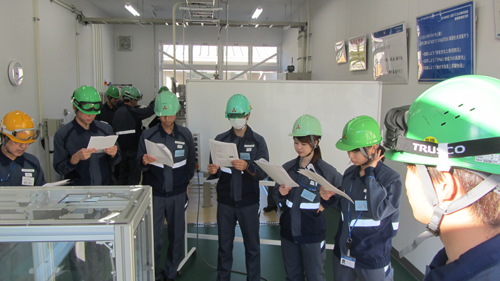
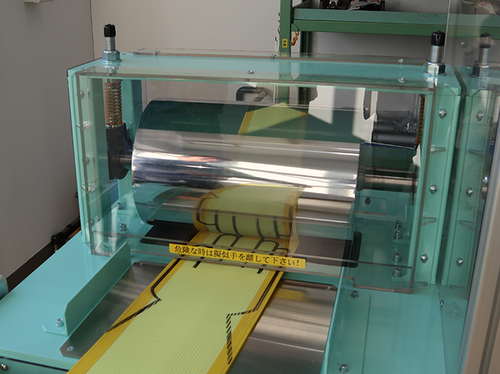
コンサルタントからの一言
人財育成の重要性を真に理解し、実践する
豊橋事業所とは長いお付き合いです(木村:2009年〜、中西:2013年〜)。同事業所は「継続的に人を育て続けていく」という信念のもと、長年活動を進めています。これは昨今の社会において非常に重要な概念ですが、実際に継続して実行するのは難しいのが実情です。しかし豊橋事業所は見事にそれをやり続けています。その原動力は「改善とは仕事が楽になり、生産性が上がることである」ということを全員が理解し、納得し実践しているからです。人財育成のための教育プログラム、研修施設の充実ぶりがとくに素晴らしく特筆すべきことです。今後の活動継続を心から応援しています。
木村 吉文(TPMコンサルタント)/中西 浩明(TPMコンサルタント)
※本稿はBusiness Insights Vol.68からの転載です。
社名・役職名などは取材当時のものです。
関連コンサルティング・サービス
生産・ものづくり・品質
生産現場の人、設備、材料、製造方法とマネジメントシステムを改善して生産性向上をはかります。生産現場は製品特性や製法により多種多様の特性を持つ複雑系です。そのため私たちは、現場でじっくり見て聞いて、フィットする特別な改善プログラムを作ることから仕事を始めます。少しだけ時間はかかりますが、そのことは現場力を高め、現場の一人ひとりが成長を感じられる魅力的な職場になることを知っているからです。